
Заточка токарных резцов есть нужной и серьёзной операцией для любого мастера, имеющего в собственной мастерской токарный станок по металлу. Так как нет ничего вечного а также самый жёсткий сплав со временем изнашивается и режущие кромки твёрдосплавных пластинок затупляются и их нужно восстанавливать. Как это грамотно сделать и посредством чего и будет детально рассмотрено в данной статье.
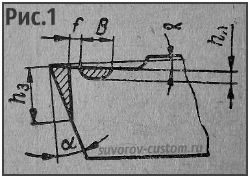
Схема износа токарного резца:
h3 — износ по задней поверхности; В — ширина лунки износа по передней поверхности; hл — высота лунки износа; f — фаска на передней поверхности.
При токарной обработке металла (точении), в следствии трения стружки о переднюю трения детали и поверхность резца о его заднюю поверхность в зоне резания, появляется высокая температура (и трение) и токарные резцы неспешно изнашиваются по задней поверхностям и передней — см. рисунок 1.
И в то время, когда износ резца превышает максимально допустимую величину (которая продемонстрирована чуть ниже в таблице величины допустимого износа) резец нужно перетачивать, в противном случае обычной токарной обработки подробностей не добьёшься.
На промышленных фирмах доводка и заточка резцов есть важной операцией, которую делают особые работники — заточники.
Но любой токарь, а тем более домашний мастер, имеющий в собственной мастерской такое счастье, как токарный станок, в обязательном порядке обязан мочь грамотно заточить и довести токарный резец собственными руками.
Главная схема заточки токарных резцов продемонстрирована на рисунке 2 чуть ниже. Из рисунка видно, что главная заточка выполняется по задним поверхностям, а дополнительная заточка выполняется по передней поверхности.
Для новых резцов на фабриках принята заточка двойных углов по передней тройных углов и поверхности по основной задней поверхности.
Но возвратимся к рисунку 2, предварительная заточка передней поверхности продемонстрирована на рисунке 2 а и она производится по всей плоскости, под углом ?1 напайки пластинки на державку резца, и данный угол делается бoльшим, чем заданный передний угол. А заданный угол ? (см. рисунок 2 б) приобретают чистовой доводкой и заточкой части передней поверхности, которая прилегает к режущему лезвию по узкой фаске.
Заднюю поверхность резца затачиваем за три операции:
первая из которых продемонстрирована на рисунке 2 в, в том месте продемонстрирована заточка резца по державке, под углом ?+ 5?. вторая операция продемонстрирована на риснуке 2 г — это заточка режущей пластинки под углом ? + 2?. третья операция продемонстрирована на рисунке 2 д — это получение заданного угла ? доводкой части задней поверхности, которая прилегает к режущей кромке по фаске f.
При ручной заточке токарных резцов их устанавливают на заточном станке под заданными углами (по отношению к абразивному кругу) посредством подкладок, установленных между опорным столиком и резцом станка (наждака) и пример таковой заточки продемонстрирован в видеоролике чуть ниже.
Но оптимальнее создавать ручную заточку на заточном станке, что имеет регулируемый по высоте и по углу поворота столик (подручник). Доработать столик возможно как продемонстрировано на рисунке чуть ниже, в том месте продемонстрировано, как доработал я упорный столик на своём заточном станке. Детально о разных заточных станках возможно почитать вот тут.
Усовершенствованный упорный столик заточного станка.
В случае если доработать упорный столик, как продемонстрировано на рисунке, то возможно не применять подкладки под резец (каковые необходимо будет изготавливать нужной толщины под различные державки резцов), а просто следует выставить столик на нужной высоте и под нужным углом заточки (ну и расстояние между кругом и столиком должно быть приблизительно 1 мм) и останется резец на столик и создавать заточку под заданным углом.
При заточке режущая кромка резца обязана пребывать на линии центра станка, либо на 3 — 5 мм ниже центровой линии. А дабы избежать захватывания токарного резца абразивным кругом, сам круг должен иметь направление вращения на пластинку резца, другими словами при заточке токарного резца, его нужно располагать относительно круга так, дабы круг прижимал пластинку к державке резца, а не отрывал её. Сохраняю надежду с этим ясно, идём дальше.
При заточке токарных резцов весьма нужно использовать охлаждающие жидкости, каковые подаются в зону обработки постоянной струёй. Так как при периодическом окунании резца в охлаждающую жидкость, происходят перенапряжения в структуре материала и появляются микротрещины.
Заточку ведём с лёгким нажимом токарного резца на абразивный круг, наряду с этим весьма нужно всегда перемещать резец на протяжении рабочей поверхности круга (если она шире либо уже затачиваемой кромки резца), дабы исключить неравномерный износ плоскости абразива, и что бы добиться ровной поверхности режущей кромки резца.
Контроль углов заточки токарных резцов посредством шаблонов:
а — контроль главного угла в плане, б — главного заднего угла, в — вспомогательного угла в плане, г — вспомогательного заднего угла, д — переднего угла, е — радиуса закругления вершины.
Геометрию затачиваемого резца контролируют на солидных фабриках особыми устройствами.
Нам же в собственной мастерской несложнее всего проконтролировать углы заточки посредством шаблонов (см. рисунок 3), каковые возможно приобрести, либо изготовить из листового металла.
Но при изготовлении шаблона лучше применять сталь, которая калится, и тогда по окончании закалки шаблон прослужит весьма долго. Перед закалкой шаблона, в металлической пластинке делаем вырезы с разными самые ходовыми углами (см. рис.3).
Уровень качества проверки зависит от точности изготовления шаблона, от квалификации токаря, ну и конечно же от его зрения. На рисунке 3 продемонстрированы углы заточки токарного резца, каковые направляться осуществлять контроль при заточке.
Применяемые абразивные круги для заточки токарных резцов.
Заточка токарных резцов по державке и под углом ? + 5? (см. рисунок 2 в) производится электрокорундовым кругом с твёрдостью 40-50 и зернистостью СМ1 и СМ2 (круги от обычного производителя имеют соответствующую маркировку), при окружной скорости круга 25 метров в секунду.
Предварительная заточка производится кругами из тёмного карбида кремния с твёрдостью 25-40 и зернистостью М3 — СМ1. Ну а окончательная заточка производится посредством кругов из зелёного карбида кремния, каковые имеют зернистость 16 — 25 и с такой же твёрдостью М3 либо СМ1.
Характеристики заточных кругов для твёрдых сплавов и сталей кроме этого обрисованы в таблице режимов заточки токарных резцов.
В том месте же указаны окружные заточные вращения станки и скорости кругов.
на данный момент окончательную заточку оптимальнее создавать посредством алмазного круга (их уже несложно отыскать в продаже), особенно для твердосплавных пластинок (металло либо минерало-керамических пластинок). Окружная скорость круга при ручной предварительной и окончательной заточке должна быть не более 12 — 15 метров в секунду.
Об доводке и алмазной заточке резцов я ещё добавлю кое что ниже и напишу из-за чего алмазная заточка лучше и предпочтительнее, чем заточка электрокорундовыми (карборундовыми) кругами. Так же ниже я напишу в каких случаях направляться применять алмазные круги, а в каких карборундовые круги.
И ещё несколько нужных советов при заточке отрезных резцов, рекомендую взглянуть в видеоролике чуть ниже.
Доводка токарных резцов.
По окончании заточки токарных резцов, их подвергают доводке карбидом бора, на чугунном диске, что вращается со скоростью 1 — 2 метра в сек. Вращение диска должно быть направлено от опорной поверхности доводимого резца к его режущим кромкам. А режущая кромка резца (при доводке) обязана размешаться на уровне центра диска, либо мало ниже его.
Сам процесс доводки токарных резцов содержится в последовательной притирке режущих поверхностей и лезвий резца, начиная с задней и заканчивая передней, доведения и удаления шероховатостей их до зеркального блеска. Из-за чего до блеска и из-за чего доводка так нужна.
Да по причине того, что в ходе токарной обработки (как я написал выше) износ и затупление резца происходит от трения пластинки о стружку и о подробность, а чем совершеннее поверхность пластинки резца (меньше её шероховатость и выше класс чистоты поверхности) тем меньшее трение появляется в ходе точения и тем продолжительнее резец не тупится (увеличивается стойкость инструмента).
Доводка резцов производится абразивными пастами на базе карбида бора и содержится в следующем. На доводочный диск (правильнее на его рабочий торец), что возможно приобрести, а возможно и изготовить (кстати для окончательной доводки, диск возможно изготовлен не из чугуна, а из металла и обклеен кожей), перед доводкой смачиваем керосином и наносим в зигзагообразном направлении абразивную пасту 1 и после этого подводим резец 2 к диску — см. рисунок 4.
При применении керосина возможно применять всем известную пасту ГОИ (национальный оптический университет), но современные пасты применяют без керосина, поскольку они жидкие и готовы к применению по окончании взбалтывания. К тому же пасту ГОИ различной зернистости (особенно большой) отыскать на данный момент не так легко в продаже.
Исходя из этого вместо пасты ГОИ рекомендую приобрести комплект НШКК-6 от компании «Grinderman» (она же создаёт хорошие разные круги и заточные станки), что стоит приблизительно 800 рублей и что рекомендован для доводки резцов.
Он имеет несколько флакончиков шлиф-зерна карбида кремния (F60, F120, F230, F400, F600, F1000) всего 6 флакончиков, любой из которых содержит 200 грамм доводочной пасты различной зернистости.
Нужно дабы при доводке резец был закреплён жёстко в особом приспособлении, но при верно установленном столике (подручнике) и хорошо прижатом к нему резцом, возможно добиться хорошего результата и без приспособления.
Столик подручника должен быть выставлен под заданным углом доводимой поверхности резца (контролируем угломером либо шаблоном) и столик должен быть установлен с таким расчётом, дабы режущие лезвия резца (при их доводке) размешались мало ниже либо на уровне центра доводочного диска. Ну а направление вращения диска при доводке резца должно быть обратным направлению вращения заточного круга, другими словами доводочный круг обязан вращаться от державки к пластинке резца.
При его доводке и прижатии резца, зёрна абразивной пасты неспешно размельчаются, и проходя через режущие поверхности инструмента не создают сколов либо царапин, а лишь только сглаживают шероховатости от предварительной заточки резца.
Для более качественного процесса доводки и для его ускорения, и для полного применения всей поверхности диска (дабы исключить неравномерный износ диска) нужно всегда передвигать резец на протяжении поверхности диска в радиальном направлении (по отношению к доводочной плоскости диска).
На данный момент показалось в продаже огромное количество алмазных кругов. доводка и Алмазная заточка есть очень действенным средством увеличения стойкости режущих инструментов.
И при алмазной заточке твёрдосплавных резцов, чистота режущих поверхностей резца (если сравнивать с заточкой корундовыми кругами) увеличивается на 2 класса. Наряду с этим ещё и возрастает производительность, а число вероятных переточек токарных разцов увеличивается аж на 20 — 30 процентов.
Ну и для заточки токарных резцов из быстрорежущих сталей (и для их доводки) алмазная заточка выясняется более действенной и предпочтительной, поскольку достигается чистота поверхности 9 — 10 классов и как я уже писал выше, чем выше класс поверхности, тем медленнее резцы тупятся, другими словами увеличивается их стойкость.
Но направляться учесть, что алмазную заточку инструмента направляться создавать лишь имея припуск на заточку не более 0,2 мм.
В то время, когда припуск на обработку больше указанного мной тут значения (0,2 мм) экономически более удачна заточка карборундовым кругом, с доводкой и последующей заточкой алмазным кругом, для которого припуск на доводку в большинстве случаев равен всего 0,05 — 0,08 мм.
Чистоту доведённой поверхности резца контролируем посредством сравнения с резцами эталонами (эталон возможно забрать, к примеру приобретя какой то новый резец от авторитетной компании), а геометрию резца контролируем посредством шаблонов (либо посредством особого прибора, у кого он имеется). В зависимости от конструкции шаблона, токарные резцы контролируют вручную, либо на особой подставке.
В случае если проверка производится вручную, то очевидно резец держат в руке и к контролируемой плоскости (поверхности) прикладывают шаблон и наблюдают на просвет, наоборот источника света. При верной заточке токарного резца и его доводке, контролируемый угол обязан всецело совпадать с кромками шаблона и между ним и пластинкой резца не должно быть просветов.
У кого ещё нет заточного станка (говоря несложнее наждака) для заточки собственных резцов, то как изготовить станок собственными руками рекомендую почитать вот в данной статье, в том месте я обрисовал несколько вариантов, от самого несложного до опытного.
Вот помой-му и всё, в случае если что нибудь ещё отыщу в памяти о заточке токарных резцов и о их доводке, то в обязательном порядке допишу, удач всем мастерам.