
Как сделать самодельный торцеватель труб.
В практике любого гаражного мастера, любящего всё делать собственными руками, либо кастомайзера, переделывающего либо изготавливающего раму с нуля, довольно часто приходится сваривать между собой трубы разных диаметров. Но вот перед сваркой труб, их нужно подогнать между собой, и нужно с минимальными и ровными по всему стыку зазорами. Сделать это посредством простой болгарки в случае если и быть может, то продолжительно и утомительно.
Особенно в случае если таких подгонок необходимо сделать пара. Для стремительной и правильной подрезки труб под нужный диаметр, существует нужное приспособление, именуемое торцевателем. В данной статье мы разглядим, из чего возможно сделать торцеватель труб собственными руками.
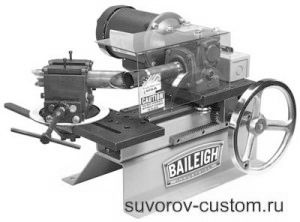
на данный момент уже стали появляться в продаже фирменные торцеватели заводского изготовлени, но цена их не всем по карману(кое-какие стоят пара сотен $, к примеру как на фото слева), а весьма недорогие изделия продолжительно не проработают. Возможно само собой разумеется торцануть трубы и посредством токарного станка, но он имеется далеко не у всех, да и для закрепления труб в станке, всё равняется нужно будет делать самодельное зажимное приспособление, но так же как и для сверлильного станка.
И раз мы уже заговорили о сверлильном станке, то тем у кого он имеется, то возможно будет изготовить один из вариантов универсального торцевателя, что сможет трудиться и как приставка к сверлильному станку, и как вариант для дрели, в случае если необходимо будет трудиться вне гаража. И габариты этого торцевателя будут всецело зависеть от габаритов вашего сверлильного станка.
База для того чтобы приспособления (см фото 1), это железный лист, толщиной 8 — 10 мм, вырезанный по форме приблизительно как на фото, причём размеры зависят от габаритов вашего станка.
В верхней части пластины необходимо осуществить паз, в котором будет закрепляться корпус подшипников вала. Корпус подшипников делается из металлического бруска, но возможно применять и дюраль, латунь, латунь.
В бруске необходимо будет высверлить сквозное отверстие для игольчатых подшипников, изображённых на фото 2 и фото з. Диаметр сквозного отверстия в бруске, зависит от наружного диаметра обоймы подшипников, какие конкретно вы отыщете, и от диаметра вала также.
Но лучше само собой разумеется отверстие для подшипников заказать фрезеровщику, дабы он выбрал его фрезой, строго параллельно нижней плоскости бруска (той которая прилегает к пазу в пластине). Причём сперва сверлится отверстие чуть меньшего диаметра подшипников, а с краёв уже выбираются отверстия чуть большего диаметра, каковые равны диаметрам подшипников.
Это разрешит в середине бруска, на глубине равной ширине игольчатого подшипника, взять ступень в 1,5 мм, дабы подшипники упёрлись в эту ступень и не проваливались глубже чем нужно.
А с обоих краёв отверстий в бруске (на глубину 7 мм) ещё нужно выбрать фрезой и отверстия большего диаметра, для сальников, каковые намного продлят жизнь подшипников (все отверстия возможно сделать и на токарном станке, и нужно за один проход). Кстати эти сальники, при плотной их запрессовке, не разрешат игольчатым подшипникам выпадать из собственных отверстий.
Не смотря на то, что, в случае если обратить внимание на игольчатые подшипники на фото 3, то легко подметить, что по середине наружной обоймы проточена канавка для подвода смазки. Эту канавку возможно применять и для фиксации подшипника в корпусе.
Необходимо будет просверлить в корпусе отверстие (наоборот каждого подшипника) в котором нарезается резьба и после этого вворачивается остро заточенный фиксирующий винт (для каждого подшипника), что упрётся в канавку (и в отверстие для смазки) в наружной обойме подшипника и зафиксирует подшипник на своём месте.
Но однако в обязательном порядке необходимо попытаться (токарю либо фрезеровщику) при обработке отверстий корпуса, дабы при последующей запрессовке, обоймы подшипников зашли хорошо в собственные отверстия в корпусе.
Время от времени возможно будет выкручивать фиксирующие винты, и заливать в отверстие мало масла, для смазки роликов. Так как в обойме имеется особое отверстие (см фото 3), для подвода смазки к роликам.
В нижней плоскости бруска (корпуса подшипников), той что прилегает к плоскости пластины торцевателя, направляться просверлить несколько отверстий и нарезать в них резьбу М10.
После этого в эти отверстия на клею вкручиваются шпильки с резьбой М10. Останется засунуть корпус подшипников шпильками в паз пластины, и зафиксировать барашковыми гайками. Протяженность паза в пластине, разрешит мало изменять (сдвигать вверх) положение корпуса подшипников, что время от времени не редкость полезно, в случае если необходимо зажать трубу громадного диаметра (как на фото 8).
Вал, на котором будет крепиться корончатая фреза, возможно заказать токарю из жёсткой стали, но лучше применять готовый вал от амортизаторной стойки подвески машин (возможно поискать на авторазборке).
Главное преимущество штока амортизатора, это то, что он уже имеет жёсткое и полированное покрытие, и будет, прекрасно скользить в подшипниках, и медлительно изнашиваться. Но необходимо будет поискать шток амортизатора, с наружным диаметром под внутренний диаметр как раз ваших игольчатых подшипников.
В самой верхней части штока, необходимо осуществить выборки, дабы оказался шестигранник (как у корончатой фрезы на фото 4), это не разрешит штоку проворачиваться в патроне сверлильного станка.
Как закрепить корончатую фрезу на штоке? Имеется пара вариантов, и самый простой — это совершенно верно просверлить ( лучше на токарном станке) в нижнем торце штока отверстие, диаметром как и шестигранник корончатой фрезы, а после этого с боков штока просверлить несколько отверстий (с резьбой) для винтов, каковые будут зажимать шестигранник фрезы в отверстии и фиксировать его от проворота.
При втором варианте, возможно сделать саму конструкцию чуть выше, и проточить нижнюю часть штока и нарезать в том месте резьбу (либо конус) для мелкого патрона от дрели. Данный вариант я считаю лучше, поскольку он разрешает надёжней закреплять фрезу, и скоро её поменять. Но данный вариант делает торцеватель чуть выше, и он в мелкий сверлильный станочек может не влезть. Но как вариант применения торцевателя без сверлильного станка (либо с громадным станком) данный вариант я считаю лучшим. Тем более, что новый патрон от дрели возможно приобрести на данный момент весьма дёшево (приблизительно 5 — 7 $).
Потом необходимо осуществить в пластине круговой паз, в котором будет крепиться зажим для труб, и данный круговой паз разрешит поменять угол зажима трубы. Рядом с пазом, полезно наклеить транспортир, что окажет помощь видеть угол закрепляемой трубы, но возможно нанести и собственные метки, по которым вы значительно чаще станете торцевать трубы, к примеру для угла рулевой колонки рамы мотоцикла.
Зажим для труб легко изготовить из куска П- образного профиля (возможно вырезать из квадратной трубы), но лучше применять кусок швеллера (шириной 80 — 100 мм), он намного тверже.
А сбоку к куску вырезанного швеллера, приваривается кусочек железной шпильки и пластины, благодаря которой трубный зажим будет крепиться к пластине (в полукруглом пазу).
Ну, а сам хомут для труб, с резьбовым штоком, возможно изготовить самому, из брусочка с отверстием в центре и резьбой для штока, и металлической ленты, закрепляемой на брусочке четырьмя винтами. А возможно приобрести готовый съёмник, для выдавливания поршневого пальца (для мопеда) из поршня ( на фото 5, продемонстрирован изготовленный мной за несколько часов съёмник поршневого пальца).
Сейчас необходимо будет внизу пластины приварить строго перпендикулярно (под 90 градусов) пластину либо кусок уголка с отверстиями, каковые разрешат закрепить торцеватель в пазах станины сверлильного станка. В случае если же таковой торцеватель труб будет употребляться без сверлильного станка, то тогда приваривать перпендикулярно пластину не требуется.
Нужно всего лишь просверлить отверстия в пластине, дабы закрепить торцеватель посредством болтов, положив его на столе либо верстаке.
Это был обрисован универсальный торцеватель, что возможно применять как на сверлильном станке, так и просто на столе. Но в случае если же у кого то нет сверлильного станка, то возможно изготовить ещё более простой торцеватель, продемонстрированный на фото 6. Тут не требуется будет копаться с полукруглым пазом, и употребляться будут всего две 10 — 12 миллиметровые железные пластины, корпус подшипников и зажим для труб.
Причём в качестве зажима возможно применять струбцину либо две струбцины, закреплённые на одной из пластин. В том месте где пластины стыкуются между собой болтом, также полезно нанести градусные риски.
Но лучше само собой разумеется изготовить струбцину замечательнее, такую как на фото 6. Корпус подшипников делается так же как я обрисовал выше, но возможно закруглить его сверху как на фото, но это не обязательно.
И наряду с этим варианте лучше для закрепления фрезы применять патрон от дрели, поскольку места тут большое количество и габариты не ограничены габаритами сверлильного станка. Кстати для вращения вала этого торцевателя, возможно применять не только простую дрель, но и закрепить такое устройство на место суппорта токарного станка, и вал зажать в патрон станка. Устройство переносное (мобильное) и весит не большое количество, и его возможно закрепить не только к верстаку, но кроме того к табурету.
На той части штока, которая будет зажиматься в патрон дрели либо токарного станка, как я уже сказал, лучше сделать не круглый вал, а шестигранный.
Это исключит проворачивание вала в патроне, поскольку нагрузка на фрезу при обработке не маленькая. Но обороты не нужно делать громадные, поскольку при громадных оборотах возможность скалывания зубьёв фрезы больше.
Фрезы на данный момент продаются в комплектах (фото 7), но возможно приобрести и поштучно. Причём корончатой фрезой мелкого диаметра, возможно сверлить в трубах отверстия, и причём намного действеннее чем сверлом.
Надеюсь, что какой то вариант самодельного торцевателя для труб, обрисованных в данной статье, заинтересует кого то из гаражных умельцев, и в случае если кто то изготовит подобное устройство, то намного облегчит и ускорит процесс изготовления любых трубчатых конструкций; удачи всем.