
Дисковые тормоза в первый раз заменили менее действенные барабаны в далёком 1958 году, в то время, когда французкая компания Ситроен, в первый раз в мире применила диски из чугуна на легендарном серийном Ситроене — DS19. И до сих пор принцип остановки транспортного средства остаётся прошлым: кинематическая энергия движущегося мотоцикла либо автомобиля преобразовывается в тепло, которое в воздухе. Скоростные показатели транспорта неспешно росли, и пропорционально квадрату скорости росла и энергия выделяющегося тепла, и с каждым днём её становилось всё больше. И наступил момент, что кроме того открытый встречному ветру чугунный тормозной диск, начал перегреваться.
Показались двойные тормозные диски с крыльчаткой в (вентилируемые диски), на спортивных автомобилях стали делать воздухозаборники, направляющие воздушный поток прямо на тормозной диск, но на скоростях за 200, и это не помогало, и перегретый чугунный диск, терял собственную сцепную эффективность.
Ситуация согрела для, понятный всем конструкторам и инженерам, что старый, хороший серый чугун, исчерпал собственные возможности.
Воспалённые взгляды конструкторов-разработчиков обратились к совсем новым материалам — композитам, либо как их ещё именуют разработчики — углепластики. Они весьма прочные (прочнее стали), лёгкие, а основное термостойкие.
Не секрет, что попытки сделать композитный тормозной диск, разработчики предприняли ещё в начале восьмидесятых годов двадцатого века, но дальше собственных опытов и ограниченного применения на практике лишь на болидах формулы 1, дело не продвинулось.
Вся обстоятельство в через чур дорогом производстве, что ощутимо било по карману кроме того богатых спонсоров формулы 1. Да к тому же требуемый для углепластиковых тормозных дисков температурный режим, что требовался для действенного торможения, выяснилось сложновато обеспечить и поддерживать.
Прорыв в производстве тормозных дисков.
И лишь совсем сравнительно не так давно, дело сдвинулось с мёртвой точки. В Гуммерсбахе, на компании Адвантек, три молодых и гениальных конструктора-разработчика вывели и внесли предложение совсем новый материал СиКом, что так звучит от производных «кремниевый композит».
Новый материал идеально подходит чтобы сделать из него лёгкий, прочный, термостойкий, и что самое основное — довольно не дорогой тормозной диск.
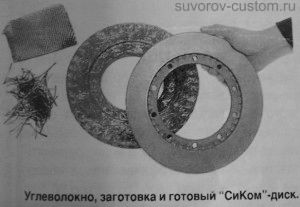
Могу предложить кроме того на странице сайта неповторимый рецепт, полученный гениальными изобретателями. Внезапно найдутся рукастые и технически оснащённые мастера, каковые в собственной мастерской сделают новейший тормозной диск.
Необходимо смешать углеволокно с содержащей углерод смолой, (консистенция чуть жиже автомобильной шпаклёвки).
Позже заполняем этим составом смазанную воском форму (форму точим практически для того чтобы размера, какой диск желаем взять, но чуть больше, покинув припуск для обработки). Ставим в печь. При нагревании полимерный состав твердеет, но получается до тех пор пока ещё довольно мягкая заготовка, но которую возможно механически обработать режущим инструментом (резцом станка).
Ну а сейчас самое основное. Необходимо поместить заготовку в вакуум, после этого нагреть до высокой температуры, (до какой, к сожалению компания умалчивает) и подвергают действию жидкого кремния. Наряду с этим происходит диффузия, а внедрившийся в углепластик кремний, неспешно преобразовывается в карбид кремния (кстати весьма жёсткий материал, что практически не уступает бриллианту).
Вот это и имеется СиКом.
Данный материал состоит на 75 — 85 процентов из углеродного волокна, и на 15 — 25 процентов из свободного кремния и карбида. Термостойкость СиКома достигает +1400 градусов, а твёрдость, как я уже сказал, практически не уступает бриллианту.
В заключении подчеркну, что разработка получения СиКома не смотря на то, что и дороже производства простых чугунных дисков, но однако не на столько как было с первыми углепластиковыми дисками для формулы 1. Но самое основное, что тормозной диск оказался в четыре раза легче простого чугунного, а это благоприятно отражается для управления и комфорта автомобили либо мотоцикла. Так как значительно снижается неподрессоренная масса и существенно значительно уменьшается гироскопический эффект колёс.
О перегреве тормозных дисков возможно будет окончательно забыть, а вот с колодками будет необходимо ещё поработать. Как раз подбором действенного материала для колодок и занимаются сейчас изобретатели. Я думаю и в состав материала для новых колодок войдёт СиКом, либо процентное его содержание. Не будем гадать, работы длятся в лабораториях и на испытательных стендах, и остаётся сохранять надежду, что итог не вынудит себя продолжительно ожидать. Так как керамические диски уже взяты, соответственно и колодки на подходе.
Поживём — заметим.