
Классическая газовая сварка ещё продолжительно будет употребляться мастерами в собственных мастерских из — за собственной дешевизны (если сравнивать с плазменными аппаратами), по крайней, мере хотя бы для нагрева либо резки металла. Газовая сварка относится к сварке плавлением. Процесс газовой сварки пребывает в нагревании кромок подробностей в месте соединения до расплавленного состояния высокотемпературным пламенем сварочной горелки.
Для расплавления и нагревания металла употребляется высокотемпературное пламя, приобретаемое при сжигании горючего газа в смеси с технически чистым кислородом. Зазор между кромками заполняется расплавленным металлом присадочной проволоки.
Газовая сварка имеет следующие преимущества : метод сварки относительно несложен, не требует сложного и дорогого оборудования, и основное, источника электричества, что принципиально важно для работ на выезде (вне мастерской).
Изменяя тепловую его положение и мощность пламени относительно места сварки, сварщик может в широких пределах регулировать охлаждения и скорость нагрева свариваемого металла.
К недочётам газовой сварки относятся меньшая большая нагрева зона и скорость металла теплового действия на металл, чем при электро-дуговой сварке. При газовой сварке концентрация тепла меньше, а коробление свариваемых подробностей больше, чем при электросварке. Но, при верно выбранной мощности пламени, умелом регулировании его состава, надлежащей марке присадочной хорошей квалификации и проволоки сварщика, газовая сварка снабжает получение отличных сварных соединений.
При помощи газовой сварки возможно сваривать практически все металлы, используемые в технике. Такие металлы как : чугун, медь, латунь, свинец легче поддаются газовой сварке, чем электро-дуговой. В случае если учесть ещё и простоту оборудования, то делается понятным широкое распространение газовой сварки на машиностроительных и других фабриках, в сельском хозяйстве, при ремонтных, строительных и монтажных работах, в противном случае и просто, в частном гараже. Газовую сварку так же используют: при ремонте и изготовлении изделий из тонколистовой стали — сварка баков автомобилей и мотоциклов, резервуаров маленькой ёмкости, заварке трещин, вварке заплат и др., ремонтной сварке литых изделий из чугуна, латуни, силумина; монтажной сварке трубопроводов при сантехнических работах; сварки изделий из его сплавов и алюминия, свинца и меди латуни; сварки соединений из тонкостенных труб; наплавки бронзы на подробности из чугуна и стали; сварке ковкого и высокопрочного чугуна с применением присадочных прутков из бронзы и латуни, при низкотемпературной сварке чугуна. Газовая сварка, это хорошая альтернатива для того, кто не имеет возможности себе позволить приобрести дорогою аргонно-дуговую сварку TIG AC/DC, подробнее о ней просматривайте тут.
Для газовой сварки нужны: газы — горючий газ и кислород (ацетилен); присадочная проволока для наплавки и сварки; кислородный баллон для хранения запаса кислорода; ацетиленовый либо пропановый баллоны; кислородный и ацетиленовый редукторы для ацетилена давления и понижения кислорода, подаваемых из баллонов в горелку либо резак; сварочная горелка либо резак для резки и нагрева металла; Резиновые шланги для подачи в горелку ацетилена и кислорода; принадлежности для резки и сварки — очки с чёрными светофильтрами(стёклами) для защиты глаз от броского света сварочного пламени, металлические щётки для очистки металла от коррозии, флюсы либо сварочные порошки, если они требуются для сварки данного металла.
Кислород. Кислород при обычной температуре и атмосферном давлении — газ без цвета и запаха, пара тяжелее воздуха.
При обычной температуре и атмосферном давлении 20°С масса 1 м? кислорода равна 1,33 кг. Сгорание горючих газов и паров горючих жидкостей в чистом кислороде происходит весьма энергично и с громадной скоростью, а в зоне горения начинается высокая температура. При соприкосновении сжатого газообразного кислорода с маслами либо жирами они смогут самовоспламеняться и это возможно обстоятельством взрыва.
Исходя из этого, при обращении с аппаратурой и кислородными баллонами (редукторы, горелки, резаки, шланги), нужно шепетильно смотреть за тем, дабы на них не попадали кроме того незначительные следы масел либо жиров. Для сварки и резки производят технический кислород трёх сортов: высшего сорта, чистотой не ниже 99,5%; первого сорта, чистотой не ниже 99,2% и второго сорта, чистотой не ниже 98,5% по количеству. Остаток 0,5-1,5% составляют аргон и азот.
Баллоны для кислорода и других сжатых газов являются металлические цилиндрические сосуды. В горловине баллона сделано отверстие с конусной резьбой, куда ввёртывается запорный вентиль. Баллоны окрашивают в условные цвета, в зависимости от рода газа. Кислородные баллоны — в светло синий цвет, ацетиленовые — в белый, для чистого аргона — в серый с зелёной поперечной полосой, для технического аргона — в тёмный с синей поперечной полосой, для углекислоты и воздуха — в тёмный, для водорода — в тёмно-зелёный, для других горючих газов (метан, пропан) — в красный цвет.
Верхнюю сферическую часть баллона не окрашивают и на ней выбивают паспортные эти баллона: марку завода изготовителя, тип, заводской номер, вес в килограммах, ёмкость в литрах рабочее и испытательное давление в воздухах, срок и дату изготовления следующего опробования, клеймо ОТК завода-изготовителя. Тут же выбивают клейма при испытаниях баллона и последующих осмотрах, каковые выполняют раз в пять лет.
Для подсчёта количества кислорода в баллоне, необходимо водяную ёмкость баллона в дм? умножить на давление газа в кг/ см?. К примеру, ёмкость стандартного баллона равна 40дм?, а давление кислорода 150 кг/ см?. Количество кислорода в баллоне : 40?150=6000 дм? либо 6 кубических метров, соответственно при атмосферном давлении.
Расходовать кислород из баллона возможно до остаточного давления 0,5 — 1 кг/см?. Всецело производить кислород из баллона не рекомендуется, поскольку на предприятии, где наполняют баллоны, должны удостовериться, что в баллоне был как раз кислород.
Баллоны для ацетилена, для обеспечения надёжное хранение ацетилена под большим давлением, заполняют особой высокопористой массой, которая подготавливается из древесного активированного угля, пемзы, инфузорной почвы и других пористых веществ. Массу в баллоне пропитывают ацетоном, в котором ацетилен прекрасно растворяется.
Ацетона вводят, приблизительно, 225 — 300 г на 1 дм? ёмкости баллона. Пребывав в порах массы, растворённый в ацетоне ацетилен делается взрывобезопасным и его возможно хранить в баллоне под давлением до 25 — 30 кг/см?. По ГОСТ 5457 — 60 обычное давление для растворённого в ацетоне ацетилена установлено 19 кг/см? при 20°С.
В то время, когда открывают вентиль, ацетилен выделяется из ацетона и в виде газа выходит через редуктор в шланг горелки. Ацетон остаётся в порах массы и снова растворяет новые порции ацетилена при последующих наполнениях баллона газом. В газопламенной обработке металлов ацетилен, накачиваемый в баллоны, заполненные ацетоном и пористой массой, принято именовать растворённым ацетиленом.
Применение при резке и газовой сварке растворённого ацетилена в баллонах имеет последовательность значительных преимуществ если сравнивать с ацетиленом, что приобретают в мобильных ацетиленовых генераторах (из карбида).
Это громадная безопасность работ, более высокая чистота ацетилена свободного от жидкости, что разрешает применять его при работе при минусовых температурах (зимний период), конечно, более большое давление ацетилена перед горелкой либо резаком, что разрешает использовать аппаратуру равного давления, вместо инжекторной и снабжает устойчивость сварочного и подогревательного пламени, повышает производительность труда; более компактная сварочная установка (на данный момент показались мелкие 5-ти литровые баллоны); простота обслуживания сварочной установки, что разрешает управляться одному человеку, без ассистента, что раньше обслуживал ацетиленовый генератор.
Для определения количества ацетилена в баллоне последний взвешивают до и по окончании наполнения газом. разность весов даёт количество находящегося в баллоне ацетилена в килограммах. Вес порожнего ацетиленового баллона, именуемый весом тары, слагается из суммы весов: оболочки баллона с вентилем, ацетона и пористой массы. Вес тары выбивается на сферической части баллона. Бесшовные ацетиленовые баллоны имеют те же размеры, что и кислородные.
при отборе ацетилена из баллона вместе с газом уносится 30-40 г ацетона на 1 м ? ацетилена. Это сокращает ацетиленовую ёмкость баллона при последующих наполнениях. Для уменьшения утрат ацетона из баллона не нужно отбирать более 1700 дм?/ч ацетилена, а ацетиленовый баллон на протяжении работы нужно устанавливать вертикально. При громадных расходах ацетилена пара баллонов соединяют в батарею.
По данной же причине нельзя отбирать ацетилен из баллона до остаточного давления менее 0,5 кгс/см? при температуре ниже 0°, менее 1 кгс/см? при температуре от 0до 15°С, менее 2 кгс/см? при температуре от 15 до 25°С и менее 3 кгс/см? при температуре от 25 до 35°С.
Порожние ацетиленовые баллоны по окончании израсходования из них газа должны храниться с хорошо закрытыми вентилями. Это нужно чтобы при увеличении окружающей температуры не имел возможности выделяться из баллона ацетилен в помещение , а при понижении температуры не имел возможности засасываться в баллон окружающий воздушное пространство.
Обстоятельством этого есть изменение растворимости ацетилена, оставшегося в баллоне: при увеличении температуры растворимость падает и ацетилен выделяется из раствора, а при понижении- растворимость возрастает и в баллоне создаётся вакуум.
Вентили для баллонов. Вентили кислородного баллона изготовляют из бронзы. Сталь для подробностей вентиля, соприкасающихся с кислородом, использовать запрещено, поскольку она очень сильно корродирует в среде сжатого мокрого кислорода. В кислородном вентиле, благодаря случайного попадания масла либо при воспламенении от трения фибровой прокладки сальника, вероятно загорание металлических подробностей, потому, что сталь может гореть в струе сжатого кислорода.
Латунь не горит в кислороде, исходя из этого её использование в кислородных вентилях безопасно. наружные подробности ( маховички заглушки и др. ) возможно изготовлять из стали, пластмасс и алюминиевых сплавов.
Кислородный вентиль имеет сальниковое уплотнение с фибровой прокладкой, в которую буртиком упирается шпиндель, прижимаемый пружиной, а при открытом клапане кроме этого и давлением газа. Вращение маховичка передаётся клапану через муфту, надеваемую на квадратные хвостовики клапана и шпинделя. для уменьшения трения фибровую прокладку пропитывают чистым парафином в течение 40 мин. при 70°С с последующим удалением избытка парафина.
Ацетиленовые вентили изготовляют из стали, использование которой в этом случае безопасно.
Напротив, в ацетиленовых вентилях запрещается использовать сплавы и медь, которые содержат более чем 70% меди, поскольку с медью ацетилен может образовывать взрывчатое соединение- ацетиленистую медь. К ацетиленовому вентилю редуктор присоединяют хомутом, снабжённым нажимным винтом. Шпиндель вращают торцевым ключом, надеваемым на квадратный финиш шпинделя.
Нижняя часть шпинделя имеет вставку из эбонита и является клапаном. Для уплотнения сальника используют комплект кожаных колец. В хвостовик вентиля засунут войлочный фильтр.
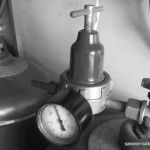
редуктор для пропана
редуктор для кислорода
Разная конструкция вентилей, как и различная окраска баллонов, даёт предупреждение возможность ошибочного наполнения ацетиленом кислородного баллона, и напротив; это воображает громадную опасность, поскольку может привести к взрыву баллона при наполнении его не тем газом, для которого этот баллон рекомендован.
Редукторы для сжатых газов. Редукторы помогают для понижения давления газа, поступающего из поддержания и баллона этого давления постоянным, независимо от постепенного понижения давления в баллоне.
Раньше при Советском ГОСТЕ (6268-68) выпускалось 18 типов редукторов, расчитанных на производительность и различные давления. основные детали и Принцип действия у всех редукторов приблизительно однообразны. Кислородный и ацетиленовые редукторы по конструкции однообразны и отличие у них только в подсоединении к баллону. Кислородный редуктор подсоединяется к баллону накидной гайкой, а ацетиленовый посредством особого хомута с винтом.
Кислородный редуктор окрашивается в светло синий цвет, ацетиленовый в белый, пропановый в красный. Ниже приводится таблица с характеристиками редукторов.
Присоединив редуктор к вентилю баллона, всецело ослабляют регулирующий винт редуктора, а после этого открывают вентиль баллона, смотря за показаниями манометра большого давления. Затем возможно устанавливать рабочее давление, вращая регулирующий винт редуктора по часовой стрелке и смотря за вторым манометром низкого давления.
В то время, когда давление достигает нужной величины(в большинстве случаев 2 — 4 кг для кислорода), возможно затевать настраивать горелку. При перерывах в работе вращают винт редуктора против часовой стрелки и производят газ из горелки, пока давление газа не будет равняется нулю по манометру низкого давления. Затем закрывают вентиль баллона.
сварочная горелка в разрезе
Советская сварочная горелка
Манометры редуктора должны быть исправны и верно показывать давление газа. Неисправный редуктор нужно сдать в ремонтную мастерскую. Запрещено ремонтировать редуктор, установленный на баллоне, поскольку это может привести к несчастному случаю.
Сварочные горелки. Сварочная горелка является основным инструментом при ручной газовой сварке. В горелки смешиваются в нужных количествах ацетилен и кислород(либо пропан, метан). Образующая горючая смесь, выходя под определённым давлением из канала мундштука горелки и с заданной скоростью сгорает, и при горении даёт устойчивое сварочное пламя.
Пламенем выходящим из канала мундштука горелки расплавляют главной и присадочный металл в месте сварки. Горелка помогает так же для регулирования тепловой мощности пламени, путём трансформации расхода горючего газа и кислорода.
От метода подачи горючего газа используют два типа конструкций горелок: инжекторные и безынжекторные . Инжекторные горелки трудятся на ацетилене низкого и среднего давлений. Подача газа в смесительную часть инжекторной горелки осуществляется за счёт подсоса его струёй кислорода, вытекающего с громадной скоростью из отверстия сопла, именуемого инжектором. Процесс подсоса газа с более низким давлением струёй газа с более большим давлением именуется инжекцией.
Схему узла смешивания инжекторной и безынжекторной горелки смотрите на рисунке 38. Для обычной работы инжекторной горелки, давление поступающего в неё кислорода должно быть 3 — 4 кг/см?, а ацетилена всего от 00,1 до 0,2 кг/см?.
Технические данные самые качественных Советских горелок приведены в таблице, и рекомендую поискать их в продаже, пускай бэушную, но обычного качества . При продолжительной работе инжекторной горелкой и сильном нагревании мундштука, инжектирующее воздействие струи кислорода ухудшается и количество поступающего в горелку ацетилена значительно уменьшается. Из за этого состав горючей смеси изменяется и появляется переизбыток кислорода. Приходится прерывать сварку и охлаждать мундштук.
Это свойство инжекторных горелок есть их значительным недочётом, и при долгосрочной работе рекомендую заменять их безынжекторной горелкой. Но нужно учесть, что для этого необходимо установить по окончании обоих редукторов регулятор ДКР-1-56 , что машинально поддерживает равные давления кислорода и ацетилена. Но напомню, что это нужно, лишь если вы планируете работать непрерывно пара часов, что не редкость весьма редко и лишь где нибудь на производстве либо в случае если вам лень иногда охлаждать мундштук инжекторной горелки.
Безынжекторные горелки отличаются узлом смешивания, а горючий газ и кислород в таких горелках поступают по каналам под однообразным давлением 0,5 — 1,0 кг/cм? и смешиваются, и после этого на выходе из сопла мундштука образуют сварочное пламя. Эти горелки снабжают постоянный состав горючей смеси кроме того в самых тяжёлых условиях работы, при сильном нагревании наконечника. Исходя из этого горелки громадной мощности и многопламенные горелки, действующий при большой температуре мундштука, предпочитают делать безынжекторными и снабжают устройствами для водяного охлаждения мундштука либо наконечники НАТ с оплёткой из асбеста, заключённой в кожух, что предохраняет их от нагревания теплом от толстой свариваемой подробности(к примеру чугунной).
Для сварки тонколистового металла( к примеру для сварки алюминиевого бака мотоцикла) от 0,2 до 4 мм при меняют облегчённые горелки ГСМ- 53(горелка сварочная малая) либо «Малютка» с набором из наконечников № 0; 1; 2; 3. Малые горелки имеют вес 360 — 400 г и вычислены на шланги диаметром 6 мм
Как мы знаем у ацетилена самая громадная температура горения, (см. таблицу горючие газы) и при резке металлов и газовой сварке возможно использовать так же и другие горючие газы, к примеру метан, пропан либо муниципальный газ и в таблице указано какой металл возможно варить либо паять жёсткими припоями посредством этих газов. Но нужно учитывать, что для расплавления металла и эффективного нагрева при газовой сварке, температура пламени обязана быть больше вдвое температуру плавления свариваемого металла. Исходя из этого применять газы заменители ацетилена целесообразно лишь при сварке металлов с более низкой температурой плавления, чем сталь, к примеру его сплавов и алюминия, латуни, свинца, конечно при пайке жёсткими припоями
При резке металла ацетилен применять не обязательно и возможно использовать те горючие газы, каковые при сгорании в смеси с кислородом дают пламя с температурой не ниже 1800°С.
Кстати для увеличения температуры пламени, возможно поискать в продаже горелку ГЗУ 2-62 с наконечником НЗП с подогревающей камерой(см рисунок 41) у которой диаметры каналов мундштука, смесительной камеры и инжектора подобраны из расчёта, что бы наконечник данного номера снабжал такую же тепловую мощность пламени, как при работе на ацетилене. Температура пламени с таким наконечником увеличивается на 300 — 360 °С, если сравнивать с горелками без подогрева. Горелками с этими наконечниками возможно сваривать сталь толщиной до 5 мм, при всех положениях шва в пространстве и создавать подогрев и сварку чугуна, и всё это осуществимо без ацетилена на распространённом пропане, метане либо природном газе.
Нужно при сварке стали пропаном либо метаном использовать сварочную проволоку, содержащую повышенное количество марганца и кремния, каковые употребляются в качестве раскислителей, а при сварке цветных металлов и чугуна, применять особые флюсы.
Обращение с горелками. Исправная и верно собранная и отрегулированная горелка обязана давать обычное устойчивое сварочное пламя. В случае если горение не ровное, либо пламя отрывается от мундштука, меркнет либо даёт хлопки и обратные удары, то направляться отрегулировать вентилями подачу ацетилена и кислорода(значительно чаще уменьшить подачу).
В случае если по окончании регулировки неполадки не устраняются, то обстоятельством смогут быть неисправности в самой горелке, в частности: неплотности в соединениях, повреждение выходного канала мундштука либо инжектора, неверная установка подробностей горелки при сборке, замусоривание каналов, износ подробностей. Для проверки исправности снимаем с штуцера ацетиленовый шланг и установив редуктором соответствующее давление кислорода(приблизительно 3 кг), открываем кислородный краник на горелке. При исправном инжекторе, в ацетиленовом штуцере должно показаться разряжение, которое легко обнаруживается приложив к штуцеру палец, что обязан присасываться. В случае если подсос имеется, то инжекторная горелка исправна.
При отсутствии подсоса, направляться разобрать горелку и мало выкрутить инжектор, поскольку величчина подсоса зависит от расстояния между входом и концом инжектора в смесительную камеру.
Вывёртывать инжектор через чур очень сильно не нужно, поскольку наряду с этим подсос будет уменьшаться. При отсутствии подсоса так же направляться проверить не засорены ли каналы мундштука, смесительной камеры, и ацетиленовой трубки, а при засорении прочистить каналы узкой бронзовой проволокой и после этого продуть их.
Перед тем как приступить к работе необходимо создать на редукторах горючего и кислорода газа нужное рабочее давление (обрисовано выше) и после этого приоткрыть кислородный вентиль на горелке и этим создать разряжение в инжекторе. В то время, когда кислород начнёт выходить из мундштука, направляться чуть открыть газовый вентиль горелки и, через пара секунд, поджечь горючую смесь у отверстия мундштука. Потом регулируют пламя, дабы светло синий язычок- ядро, был приблизительно 8 — 10 мм долгой(кислородным вентилем) и корректируют длину пламени обоими вентилями.
Долга ядра пламени в 8 — 10 мм, это примерное значение и оно зависит от номера наконечника и подробнее об этом возможно прочесть в данной статье. В случае если при зажигании смеси горелка даёт хлопок, либо при полном открытии газового вентиля в пламени не появляется избытка ацетилена, то направляться проверить прекрасно ли затянута накидная гайка наконечника, достаточно ли давление кислорода и нет ли препятствий(засорений) поступлению ацетилена в горелку(перегиба шланга либо воды в шланге).
При прекращении работы горелки, конечно при хлопках либо обратном ударе пламени необходимо постоянно закрывать сперва газовый вентиль, и лишь после этого кислородный. Если не придерживаться этого правила закрытия вентилей, то обратный удар пламени может состояться в ацетиленовый шланг. Время от времени исправная горелка по окончании весьма продолжительной работы начинает рукоплескать и давать обратные удары, это происходит от сильного нагрева мундштука.
При таких условиях необходимо погасить пламя горелки, закрытием вентилей в указанном выше порядке и охладить мундштук в сосуде с водой.